Spotfacing
When Consistency Matters
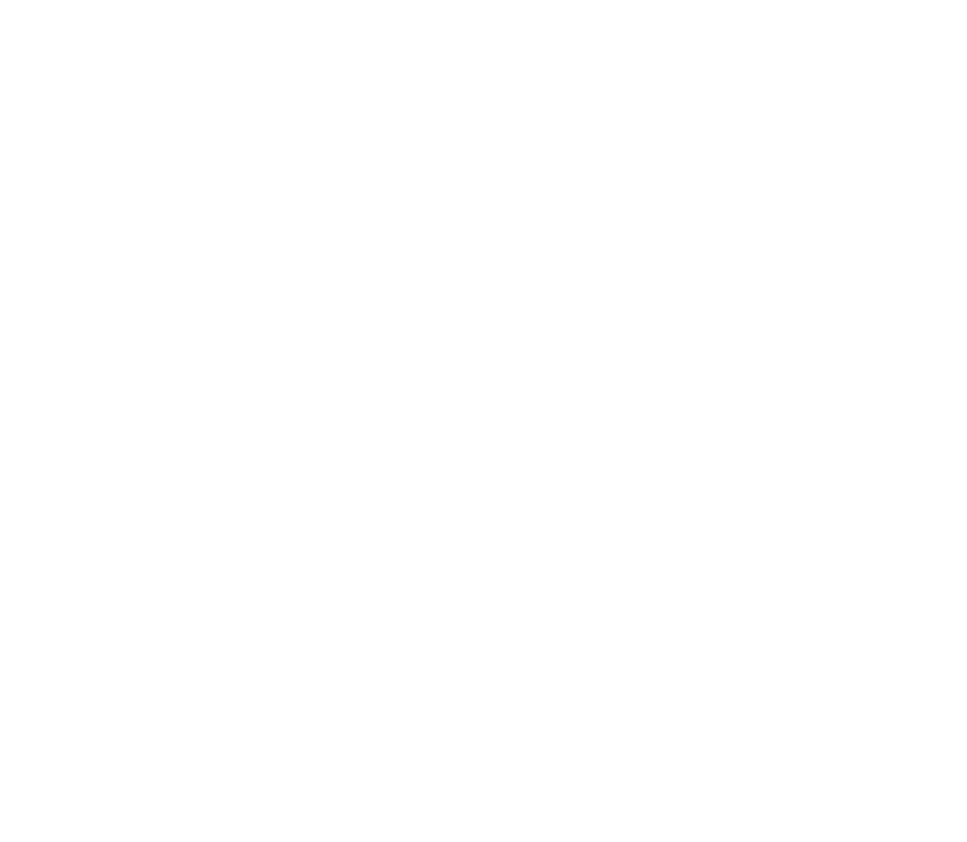
Our Spotfacing Tools
Technical specifications and tool selection
Erix spot facing tools are available for hole diameters ranging from 4.5 mm to 69 mm, with options including cylindrical and Morse taper spindles. Using high-speed steel and carbide inserts, our tools can be tailored to handle different materials and machining scenarios, providing the flexibility needed for diverse industrial applications.
What is spot facing?
Spot facing is a crucial machining process used to create a smooth, flat surface around a pre-drilled hole. At Erix Tool, our spot facing tools offer reliable solutions to achieve precise results every time. By ensuring an even and parallel surface, spot facing allows secure mounting of components like nuts, bolts, and bearings—key to product performance and longevity. We take pride in our innovative back spotface tools, engineered for consistency and precision.
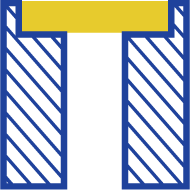
Back spotfacing tip:
How spot facing is performed with Erix Tool

Spot facing with Erix spot facing tools is both efficient and straightforward due to our smart design. Our tools feature a spindle and a unique cutting wing that folds into the spindle upon entering a pre-drilled hole. This design allows for both front and back spot facing in a single cycle, eliminating unnecessary steps and saving time and resources.
Required tools and equipment
- Smaller hole sizes: HSS wings with integrated cutting edges.
- Larger hole sizes: Carbide inserts of ISO K20 or ISO P40 for enhanced performance.
- Heavy-duty applications: Center-locked inserts for machining stainless steel and alloys, providing extra durability for tougher materials.
Step-by-step: Spot facing
- Prepare the workpiece – Apply a few drops of light oil to the hole to ease tool guidance. Use cutting fluid when machining steel for smoother operation.
- Inspect the tool – Ensure the insert quality is intact and replace if necessary. Verify that the wing rotates freely.
- Set spindle speed – Adjust speed based on the material being machined, following the recommended guidelines.
- Feeding – Start the spindle counterclockwise, feed quickly until the wing reaches the workpiece, then reduce the feed rate to a maximum of 0.2 mm/rev to ensure proper wing deployment.
- Spot facing – With the wing rotating freely, apply the recommended feed rate. The wing will swing out using centrifugal force, creating the required surface.
- Completion – Quickly retract the tool after spot facing, reducing the feed rate to fold in the wing before fully withdrawing the tool.
Why choose the Erix back spot facing tool?
The Erix Back Spot Facing Tool is built for reliability and efficiency—vital qualities for industries where downtime is simply not an option. Thanks to a flexible wing replacement design, our tools are also cost-effective for automatic facing applications. This versatility helps eliminate time-consuming manual tasks, resulting in significant production time savings and consistent results.
Applications of spot facing
Spot facing is vital across multiple industries, including manufacturing and aerospace, where precise surfaces around drilled holes ensure secure fastening points and balanced load distribution. This process directly enhances product integrity and operational reliability.
Comparison between spot facing and counterboring
When a durable and flat surface is required around drilled holes, spot facing is often the better choice compared to counterboring. Spot facing ensures a parallel, smooth surface that is essential for proper component fitting. Erix tools make this process simple and consistent, making them perfect for a variety of applications.
Contact us for more information
At Erix Tool, we’re here to help you find the perfect back spotface tool for your requirements. Contact us today for a free consultation and discover how our high-quality spot facing tools can enhance your machining processes!
Technical information
- All Spindles from ø10 upwards (hole size) with cylindrical shanks are designed for Weldon fastening (DIN 1835B).
- All Spindles from ø10 upwards (hole size) are available with a Morse Taper (27-25-MK3) rather than a cylindrical shank.
- We recommend using our extra strong HSS wing for really tough machining projects.
- Erix Tool spotfacers are fitted with grade ISO K20 inserts as standard.
- We supply grade K20 brazed inserts for HSS spotfacing wing sizes 020 and 030 (grade P40 for steel).
- As high volumes of materials like stainless or high-alloy steel are tough on the clamping system, we supply SPMA centerlocked inserts for ≥ 060 wings with SPUN inserts.
- Spotfacers with ≥ 30 mm wings are fitted with a guide tang to ensure they remain in position even at low speeds and when milling horizontally.
- Spindles with cylindrical shanks for holes ≥10 mm have coolant through as standard.
Please refer to our catalogues* for full information about capacities, dimensions, combinations, materials and standard part details.
* Available in both metric (mm) and imperial (inches) measurements.
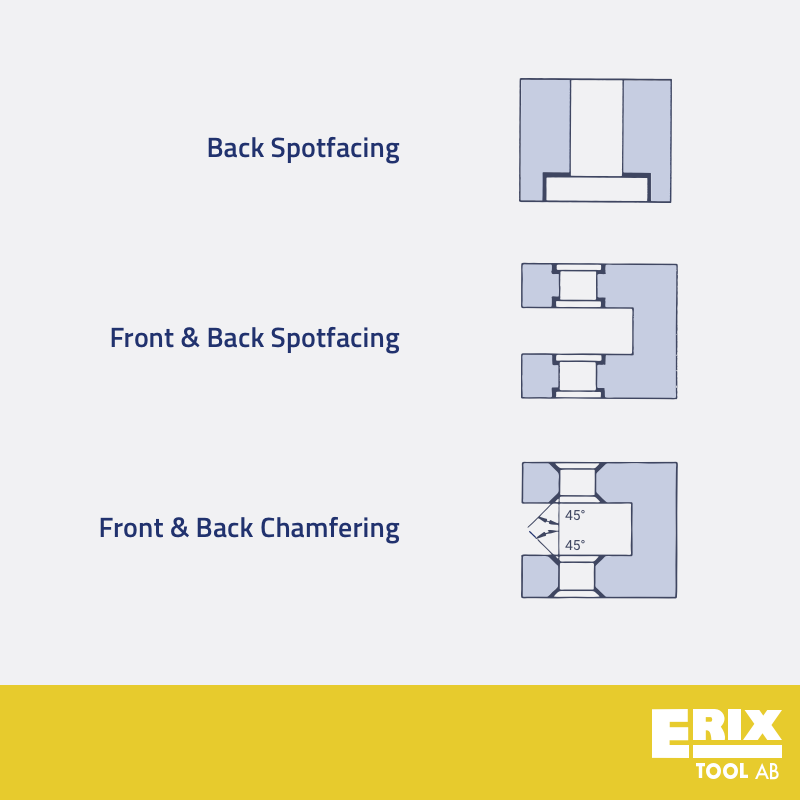
What is a spotface used for?
A spotface is used to create a flat, shallow, cylindrical surface around a hole. It serves as a landing area for components like screw heads, washers, or nuts, ensuring a stable and even contact surface.
What is spot facing in drilling?
Spot facing in drilling is a machining operation where a flat surface is created at the opening of a drilled hole. This ensures that bolts, washers, or nuts sit flush and secure against the machined surface. The tool used for this operation is called a spot facer or spot-facing tool.
What is the difference between counterboring and spotfacing?
The main difference between counterboring and spotfacing lies in their purpose and geometry:
- Counterboring: Creates a cylindrical recess with a defined shoulder at the bottom, typically for accommodating screw heads or bolts.
- Spotfacing: Produces a flat, shallow surface that is always perpendicular to the axis of the hole and is primarily used to ensure washers or bolt heads have a smooth, level seat.
How do you call out a spotface?
Spotfaces do not have a unique symbol. Instead, the counterbore symbol (⌴) is used with the addition of the letters SF (Spotface) inside the callout. The depth and diameter specifications for the spotface are typically included in the engineering drawing.
Download a Catalogue
Four good reasons
Robust & durable
The Erix cutting tool’s solid dependability is ideal for situations where downtime is unacceptable.
Simple & user friendly
A simple, rapid cutting wing replacement system makes the Erix cutting tool extremely efficient and user-friendly.
Versitile & convenient
With cutting wing sizes ranging from 8 mm to 15.6 cm few cutting tools are as versatile as the Erix Tool.
Manual & automated
Find a distributor
The Erix Tool is available through a large network of authorised
distributors and agents around the world