Counterboring
When Simplicity Matters
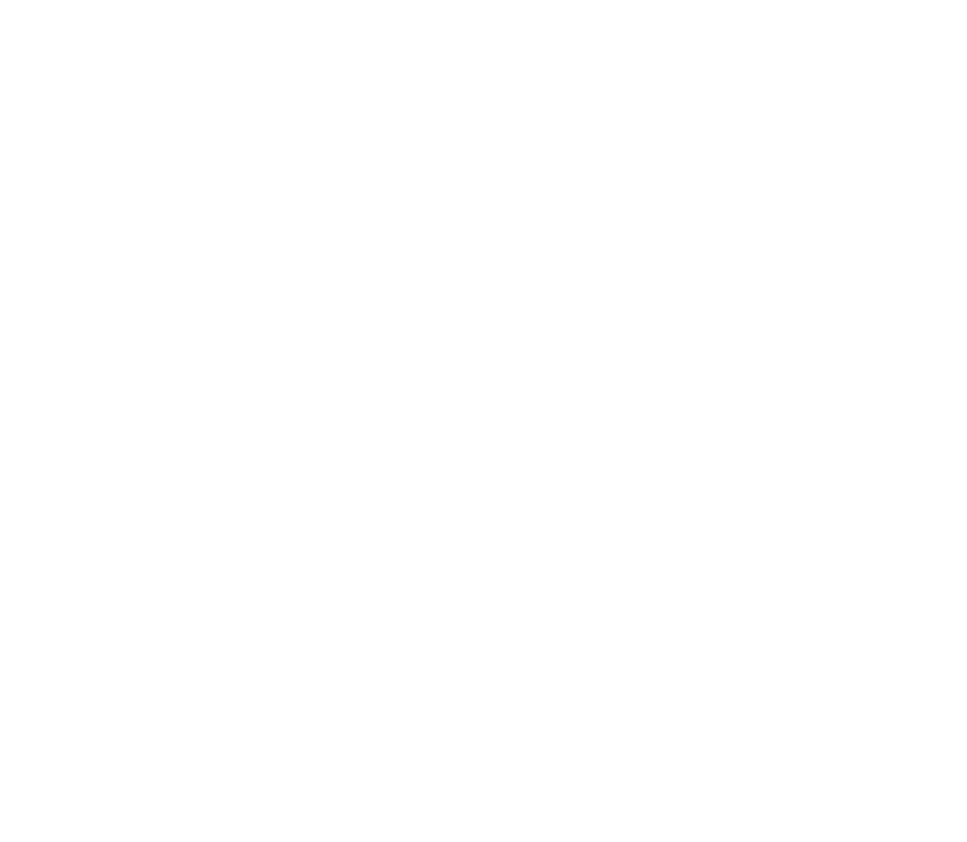
The Erix Counterbore Tool
At Erix Tool, we offer a high-precision counterbore Tool that is designed to meet the demands of the most challenging machining operations. Whether you are working with metal, wood, or plastic, our tools provide exceptional accuracy and reliability, ensuring a smooth and efficient counterboring process.
Working with counterbores means creating the perfect fit for screws and bolts, where the head sits flush with, or below, the surface of the workpiece. This method is crucial not only for functionality but also for aesthetics and safety across various manufacturing fields, from the automotive industry to precision mechanics.
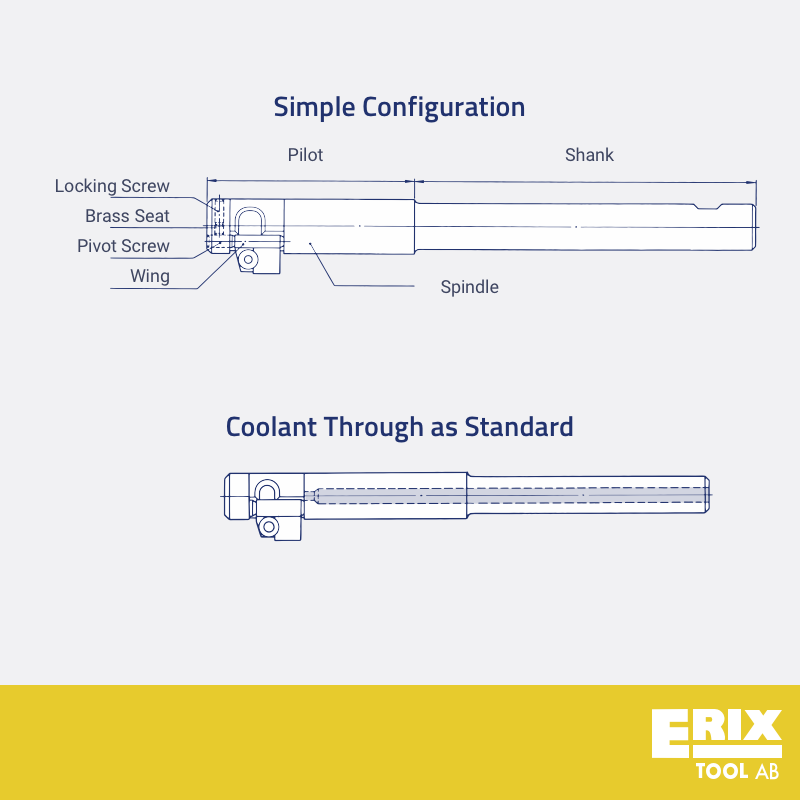
Counterboring tip:
When counterboring, always choose the right tool material for your application—steel for tough materials, HSS or carbide for harder metals. This ensures durability, precision, and a smoother machining process.
What is a Counterboring Tool?
A counterbore is a cylindrical hole with a flat bottom that allows fasteners, like screw heads, to sit neatly embedded in the workpiece. This is essential in applications where a clean finish is important, preventing the fastener from protruding and ensuring a smooth surface.
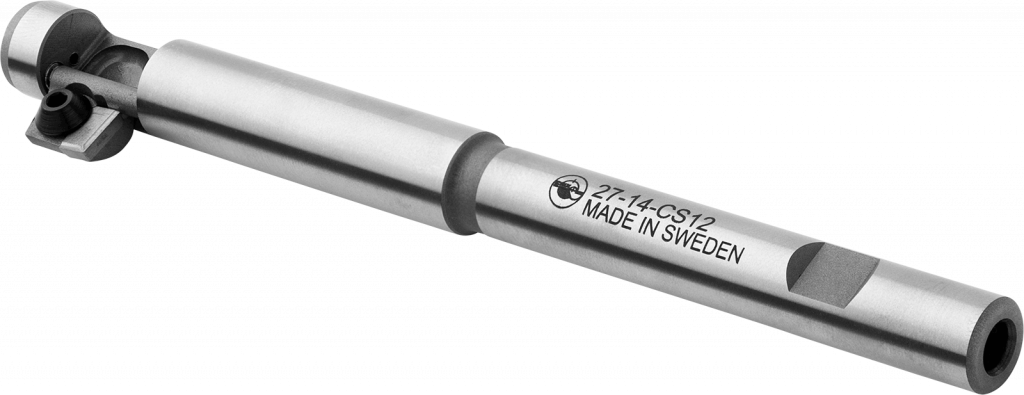
How Does the Counterboring Process Work?
The counterboring process is straightforward but requires attention to detail. It starts with selecting the right tool based on the material and dimensions of your workpiece. Our Counterbore Tool come with precise spindles and wings that ensure a perfect fit for each project.
Here’s how the process typically unfolds:
- Material selection: Choose the correct tool settings for the material you are working with, whether it’s metal, wood, or plastic.
- Measurement and marking: Accurate marking of the workpiece ensures that the hole is positioned correctly.
- Tool selection: Based on the required dimensions, select the appropriate counterboring tool from Erix Tool’s range.
- Machining: Secure the tool in the machine and begin the machining process. The counterbore tool removes material from the surface, creating a flat-bottomed hole that aligns with the original hole.
- Quality control: After machining, inspect the hole to ensure it meets the necessary specifications and standards.
Why choose Erix Tool?
Our tool are built to the highest standards, ensuring durability and precision. Whether you’re working with complex alloys or simpler materials, our tools are engineered to handle demanding tasks. Our range includes universal counterbores with interchangeable pilots, giving you the flexibility to adapt to different projects without compromising on quality.
When should you use a counterbore?
A counterbore is essential when you need to ensure a fastener sits flush with or below the surface. This is particularly important in industries where precision and a smooth finish are required, such as aerospace, heavy machinery, and automotive manufacturing.
How to specify a counterbore
Specifying a counterbore involves understanding both the dimensions of the hole and the fastener. Use the correct symbol (⌴) in technical drawings to denote a flat-bottomed hole and ensure that the counterbore matches the fastener head’s diameter and depth.
Material options for counterboring tools
Choosing the right material for your tool is key to getting the most out of your machining process. Erix Tool offers a variety of materials to suit different applications:
- Steel: Ideal for tough materials like stainless steel, steel tools provide the durability needed for high-stress environments.
- High-speed steel (HSS) and carbide: These materials offer superior cutting performance, especially when working with harder metals.
What is counterboring used for?
Counterboring is used to enlarge part of a drilled hole to a specific diameter, creating a cylindrical recess that allows the head of a bolt, screw, or fastener to sit flush with or below the surface of the material. This is particularly important in applications where a smooth surface is needed for functional or aesthetic purposes, such as in mechanical assemblies, engine components, or precision machinery.
What is the difference between boring and counterboring?
Boring is the process of enlarging an existing hole to achieve precise dimensions or improve its surface finish. Counterboring, on the other hand, involves creating a recessed or stepped area at the top of a drilled hole to accommodate the head of a fastener. While boring works along the entire depth of the hole, counterboring focuses specifically on forming the recess at the top.
What is the difference between a counterbore and a countersink?
A counterbore creates a flat-bottomed, cylindrical recess in a hole, which is typically used for fasteners with cylindrical heads, such as bolts. A countersink, in contrast, produces a conical-shaped recess designed for flathead screws, allowing them to sit flush with the surface. The key difference lies in the shape of the recess: flat for a counterbore and angled for a countersink.
What is the difference between counterboring and spotfacing?
Counterboring creates a deeper recess in a hole to accommodate fastener heads, ensuring they sit flush or below the surface. Spotfacing, however, focuses on creating a shallow, flat surface around the hole’s opening, providing a clean and even area for bolt heads, nuts, or washers to rest on without significantly deepening the recess
When should counterboring be used?
Counterboring is ideal when fastener heads need to be flush with or below the surface for aesthetic or functional reasons. It is also used when securing components with bolts or screws in assemblies like machinery, engines, or structural parts. Additionally, counterboring is beneficial when clearance is needed for tools or other parts to move freely over the fastener or when precise alignment and secure fastening are essential in high-stress applications.
Download a Catalogue
Four good reasons
Robust & durable
The Erix cutting tool’s solid dependability is ideal for situations where downtime is unacceptable.
Simple & user friendly
A simple, rapid cutting wing replacement system makes the Erix cutting tool extremely efficient and user-friendly.
Versitile & convenient
With cutting wing sizes ranging from 8 mm to 15.6 cm few cutting tools are as versatile as the Erix Tool.
Manual & automated
Find a distributor
The Erix Tool is available through a large network of authorised
distributors and agents around the world